Workplace tips for safer handling of soiled shop rags and absorbents
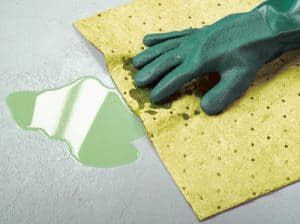
Discover how to safely deal with soiled absorbents in your workplace
From rags and fabric wipes to granular, boom, pillow, or sock absorbents, there are dozens of different products designed for handling workplace clean-up tasks. But what happens to these products after they are used to absorb a chemical spill?
While it may not be the most glamorous aspect of your job, proper disposal and management of these items are critical for maintaining a safe and environmentally responsible workspace.
In this post, we’ll provide you with tips, best practices, and guidance on how to handle these materials in compliance with federal regulations.
Why Proper Management Matters
Before we get into the nitty-gritty details, let’s talk about why managing used oily rags and chemical absorbents is so important. Whether you work in a manufacturing facility, a laboratory, or any other setting where chemicals are used, you likely encounter these materials regularly. And their improper management can lead to serious consequences.
- Safety: Used rags and chemical absorbents can be contaminated with hazardous substances. Failing to manage them properly can lead to accidents, fires, or chemical exposures that can harm employees and the environment.
- Environmental Responsibility: Disposing of these materials incorrectly can have a negative impact on the environment. Many chemicals can leach into soil and water, causing pollution that harms ecosystems and human health.
- Compliance with Regulations: Federal regulations, such as the Resource Conservation and Recovery Act (RCRA) in the United States, govern the disposal of hazardous waste, including used rags and chemical absorbents. Failing to comply with these regulations can result in fines and legal consequences.
Sending chemical-soaked rags and wipes to a “normal” laundry facility could result in the chemical flushing into the municipal sewer system. Likewise, simply tossing them in the trash could result in a fire due to the possibility of spontaneous combustion. As the City of Newton Massachusetts website explains:
“Oily rags that get folded or balled up and tossed on the floor have the danger of going through a process that starts with oxidation. As the oil is drying on the rag, it produces heat, and air gets trapped in the folds or balled up portions. Heat and oxygen are combined in addition to the rag, which is usually made of combustible cloth that can become a source of fuel. Heat, oxygen and fuel are all that is needed to create a fire, which is why oily rags that are not disposed of properly can create a fire that people are not prepared for.”
Reusable absorbent products, such as rags and certain types of wipes, can be effectively laundered. However, business owners should contact the laundry facility beforehand to determine whether or not they will accept them. Most industrial laundry facilities are fully trained to properly clean chemical-soaked rags and reusable wipes, allowing businesses to continue using them.
If the rag or wipe is contaminated with a “hazardous chemical other than oil,” the business owner should refer to the Environmental Protection Agency (EPA) for more information on how to properly dispose of it.
Now that we better understand the importance of proper management, let’s delve into some practical tips and best practices.
Best Practices for Managing Used Rags and Chemical Absorbent Products
1. Segregation and Labeling
One of the first steps in managing used rags and chemical absorbents is proper segregation and labeling. The EPA recommends businesses keep two separate stacks of used rags and absorbent products: one for non-hazardous chemicals, and another one for hazardous chemicals. Use clearly labeled containers or bins for each type of waste. This helps prevent cross-contamination and ensures that waste is properly categorized.
Example: In a manufacturing facility, designate color-coded bins for used rags and chemical absorbents. Use red or yellow bins for hazardous waste and green bins for non-hazardous waste. Ensure all employees are aware of the color-coding system.
2. Storage and Containment
Used rags and chemical absorbents should be stored in suitable containers that prevent leaks and spills. These containers should be kept in designated areas away from high-traffic zones.
Example: In an automotive repair shop, use sealable drums for storing used oil-soaked rags. Ensure these drums are stored in a secure, well-ventilated area to minimize fire hazards.
3. Training and Awareness
Proper training is key to ensuring that all employees understand the importance of managing these materials safely. Provide training on the identification of hazardous waste, proper handling techniques, and the use of personal protective equipment (PPE) like gloves or goggles.
Example: Conduct regular training sessions for laboratory staff on identifying and handling hazardous chemicals. Make sure they know the location of safety showers and eyewash stations in case of chemical exposure.
4. Regular Inspections
Frequent inspections are crucial to identify any issues with the storage and containment of used rags and chemical absorbents. Inspect containers for leaks, damage, or signs of deterioration.
Example: In a chemical manufacturing plant, designate a staff member to conduct weekly inspections of hazardous waste storage areas and report any problems promptly.
5. Hazardous Waste Pickup and Disposal
Once you have accumulated a sufficient quantity of hazardous waste, follow established procedures for disposal. In the United States, RCRA regulations dictate how hazardous waste must be managed, including requirements for labeling, manifesting, and using authorized disposal facilities.
Example: A pharmaceutical research laboratory contracts with a licensed hazardous waste disposal company to pick up and transport chemical waste to a licensed treatment and disposal facility.
6. Keep Records
Maintaining accurate records is essential for demonstrating compliance with regulations. Keep records of waste generation, transportation, and disposal. This documentation is crucial if you ever face an audit or inspection.
Example: Document the type and quantity of hazardous waste generated each month, along with disposal receipts and manifests, in a secure electronic or physical file.
7. Emergency Response Planning
In the event of a spill or accident involving hazardous waste, it’s essential to have a well-defined emergency response plan in place. Ensure that all employees are trained in these procedures.
Example: A chemical manufacturing facility conducts regular drills to practice spill response and evacuation procedures. Employees are familiar with the location of spill response kits and know how to use them.
Conclusion
Managing used rags and chemical absorbent products in the workplace may not be the most exciting task, but it’s undeniably crucial for maintaining a safe and compliant workplace. By following federal regulations, adopting best practices, and implementing workplace-specific examples, you contribute to a safer environment for both your colleagues and the surrounding community.
We understand that navigating the intricacies of hazardous waste management can be a daunting task. That’s why we’re here to help! At AbsorbentsOnline, we offer comprehensive solutions to make your workplace cleaner, safer, and more efficient.
Our team of experts specializes in providing advice, products, and services tailored to your specific needs. Whether you require high-quality absorbent materials, spill kits, or guidance on regulatory compliance, we’ve got you covered. Contact Travis Zdrazil at travis@absorbentsonline.com or (800) 869-9633.
This is a revision to a blog post with an original publication date of July 14, 2014.