Accidents happenโbut when your business handles chemicals, fuels, or other hazardous substances, even a minor spill can cause major disruption. From workplace injuries and regulatory fines to environmental contamination, the consequences are real.
Thatโs why developing an effective Spill Response Plan (SRP) is one of the smartest investments you can make in workplace safety and compliance. This isnโt just a policy to hang on the wallโitโs a proactive strategy that equips your team to respond with confidence when every second counts.
Letโs break down how to build a thorough and effective spill response plan for your facility, with practical steps and tools to make it happen.
What Is a Spill Response Plan?
A Spill Response Plan is a detailed guide for how your business will respond to spills of hazardous or potentially harmful substances. It outlines:
- What actions to take immediately after a spill
- Who is responsible for specific tasks
- What equipment and supplies are needed
- How to safely clean up and dispose of materials
- How to remain compliant with OSHA, EPA, and other regulations
Itโs your emergency manualโand when done right, it turns a potentially dangerous situation into a manageable one.
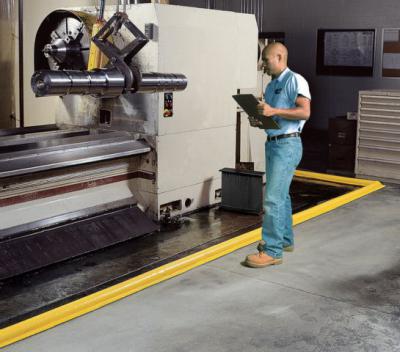
1. Start With a Facility-Specific Spill Risk Assessment
Every facility is different. Your spill response plan should be tailored to the unique layout, materials, and processes of your workplace.
Begin by identifying:
- The types of hazardous materials stored or used on-site
- The areas with the highest potential for spills (e.g., loading docks, storage rooms, chemical stations)
- The volume and concentration of substances involved
- The possible consequences if a spill occurred in each location
Refer to Safety Data Sheets (SDS) to better understand the properties and hazards of each substanceโsome may be flammable, others corrosive, or environmentally toxic.
For example, a factory that uses industrial solvents will need a different response strategy than a fleet maintenance garage that stores diesel and motor oil. Knowing the risks means you can plan and prepare accordingly.
2. Clearly Define Roles and Responsibilities
When a spill happens, every second matters. You donโt want employees scrambling to figure out who should do what.
Your plan should designate a Spill Response Team or Emergency Response Team with clearly assigned roles. Depending on your facility size and complexity, this may include:
- A team leader or incident commander, who oversees the response
- A notifier, responsible for alerting internal management or external emergency services
- A containment specialist, who handles initial control using absorbents and tools
- A cleanup crew, responsible for safe removal and disposal
- A safety officer, who ensures PPE is worn and safety protocols are followed
Every person involved should know their role before an incident occurs. And everyone else should know how to report a spill and who to notify.
Post this information prominently near workstations, spill-prone areas, and on safety boards throughout your facility.
3. Equip Your Facility With the Right Spill Response Supplies
Preparedness isnโt just about paperwork. It also means having the right gear available when itโs needed most.
Every business should have spill kits stocked and ready to deploy. These kits typically include absorbents, PPE, disposal bags, and containment tools. But not all kits are the same.
Youโll need to match your supplies to the types of spills youโre likely to encounter.
If your facility deals primarily with oil and fuel-based liquids, oil-only absorbents and kits are ideal. They repel water and soak up hydrocarbons fast. If your risks include unknown or aggressive chemicals, then hazmat spill kits (often yellow) are designed to handle those threats. For general-purpose spills, like coolants, water-based liquids, and mild chemicals, universal kits are your go-to.
Beyond kits, make sure to stock:
- Absorbent pads, socks, pillows, or booms (depending on your needs)
- Drain covers or berms to prevent spills from spreading into stormwater systems
- Chemical-resistant gloves, goggles, suits, and respirators
- Labeled disposal bags and hazardous waste containers
- Tools like dustpans, scoops, and non-sparking scrapers for solid material handling
Place kits near high-risk areasโsuch as chemical storage rooms, machinery bays, or delivery zonesโnot tucked away in a locked supply closet. Time is everything in a spill.
4. Train and Empower Your Team
Training isnโt a one-time thingโitโs an ongoing part of workplace safety. Your employees need to know not only what the plan says but how to carry it out in real life.
Effective spill response training should include:
- How to recognize different types of spills
- How to report a spill and activate the response plan
- When to evacuate and when to stay and respond
- How to properly use absorbents and deploy spill control tools
- How to put on, wear, and safely remove personal protective equipment
- What to do during cleanup and how to dispose of materials safely
In addition to classroom-style training, run practice drills for different scenarios. These drills help your team build muscle memory, test the effectiveness of your plan, and identify any gaps.
Use each drill as a learning opportunityโwhat went well, and what could be improved?
And donโt forget to document all training sessions and drills. This not only reinforces the importance of the program but also helps you stay compliant with OSHA and EPA standards.
5. Stay Compliant With Regulations
Federal and state agencies have strict requirements for spill preparedness and response. Failing to comply can lead to steep fines, lawsuits, or environmental damage.
Here are the main regulations to be aware of:
- OSHAโs Hazardous Waste Operations and Emergency Response Standard (HAZWOPER) governs employee safety during hazardous substance emergencies, including training and PPE.
- The EPAโs Spill Prevention, Control, and Countermeasure (SPCC) rule applies to facilities that store significant quantities of oil and requires a formal written plan.
- The Resource Conservation and Recovery Act (RCRA) outlines how hazardous waste must be stored, transported, and disposed of safely.
Make sure your spill response plan includes procedures that reflect these guidelines. You should also maintain:
- Updated SDS sheets for all hazardous materials
- Records of training and drills
- Documentation for any actual spill events and how they were handled
- Waste manifests and disposal receipts when dealing with hazardous cleanup materials
A strong documentation trail can be your best defense in the event of an audit or inspection.
6. Create Step-by-Step Cleanup Procedures
Once the immediate danger is addressed, thorough cleanup ensures the area is safe to re-enter and prevents future hazards. Your plan should outline exactly how this process works.
Step-by-step cleanup typically involves:
- Securing the spill area and restricting access
- Assessing the type and extent of the spill
- Containing and stopping the source
- Applying absorbents or neutralizers
- Collecting used materials and placing them in properly labeled containers
- Cleaning and decontaminating surfaces
- Ventilating the area if necessary
- Reporting the incident and reviewing the response
Proper waste disposal is a big deal. Materials that absorb hazardous substancesโlike soiled pads or glovesโcan become hazardous waste themselves and must be handled accordingly.
7. Review and Update Your Spill Plan Regularly
Your facility evolvesโnew equipment, new products, new people. Your spill response plan should evolve, too.
Set a recurring schedule to review your plan, ideally at least once per year or whenever:
- You introduce new materials or processes
- You relocate equipment or change layouts
- Key personnel change roles
- You discover gaps during drills or real incidents
- Regulatory updates require new compliance steps
Treat the plan as a living document. Involve employees in the review process, especially those who are on the front lines of potential spill zones. They often have the most valuable insights into what works in practice.
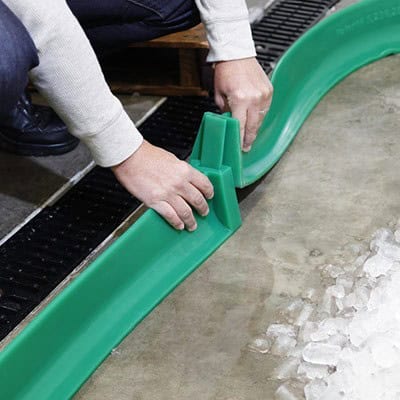
Best Practices for Long-Term Spill Readiness
Letโs wrap up with a few bonus tips to keep your business in top shape:
- Color-code your spill kits (white for oil, gray for universal, yellow for chemical) for fast identification
- Store absorbents in visible and accessible locationsโnot behind locked doors
- Keep emergency contact numbers posted near spill kits and chemical storage areas
- Work with a hazardous waste disposal service in advanceโdonโt wait until a spill happens
- Document and analyze each spill or drill to continuously improve response efforts
How AbsorbentsOnline.com Can Help You Build a Better Spill Plan
Whether youโre building your first spill response plan or upgrading an existing one, AbsorbentsOnline.com has the expertise and supplies to support your success.
We offer:
- A wide selection of high-quality spill kits tailored to oil, chemical, or universal use
- Absorbents in pads, rolls, socks, booms, and more
- Safety gear including PPE and spill containment products
- Expert advice to help you build a custom kit or plan based on your facilityโs needs
Weโre here to help you stay prepared, compliant, and safe.
Conclusion: Be Prepared, Not Panicked
Spills are a fact of life in many workplacesโbut panic doesnโt have to be. With a proactive plan, the right equipment, and well-trained employees, you can respond swiftly and safely when the unexpected happens.
Your spill response plan isnโt just about reacting. Itโs about protecting your team, your business, and your environmentโevery day. Ready to upgrade your spill kits or build a custom solution? Contact AbsorbentsOnline.com today and letโs make your workplace spill-proof.