It’s likely your business recognizes the importance of having an effective spill response plan in place. Including keeping the appropriate spill containment and clean up solutions—like spill kits—on site.
But, does your company’s response plan include regular inspections of its kits for handling spills? If not, it should. Because spill kits are not very useful if they aren’t maintained and kept in good condition!
Just how often should spill kit inspections take place? And what exactly do you need to check? Let’s dive in and take a look. Starting with a quick refresher about what kits for spills are, what they contain, and what they are used for.
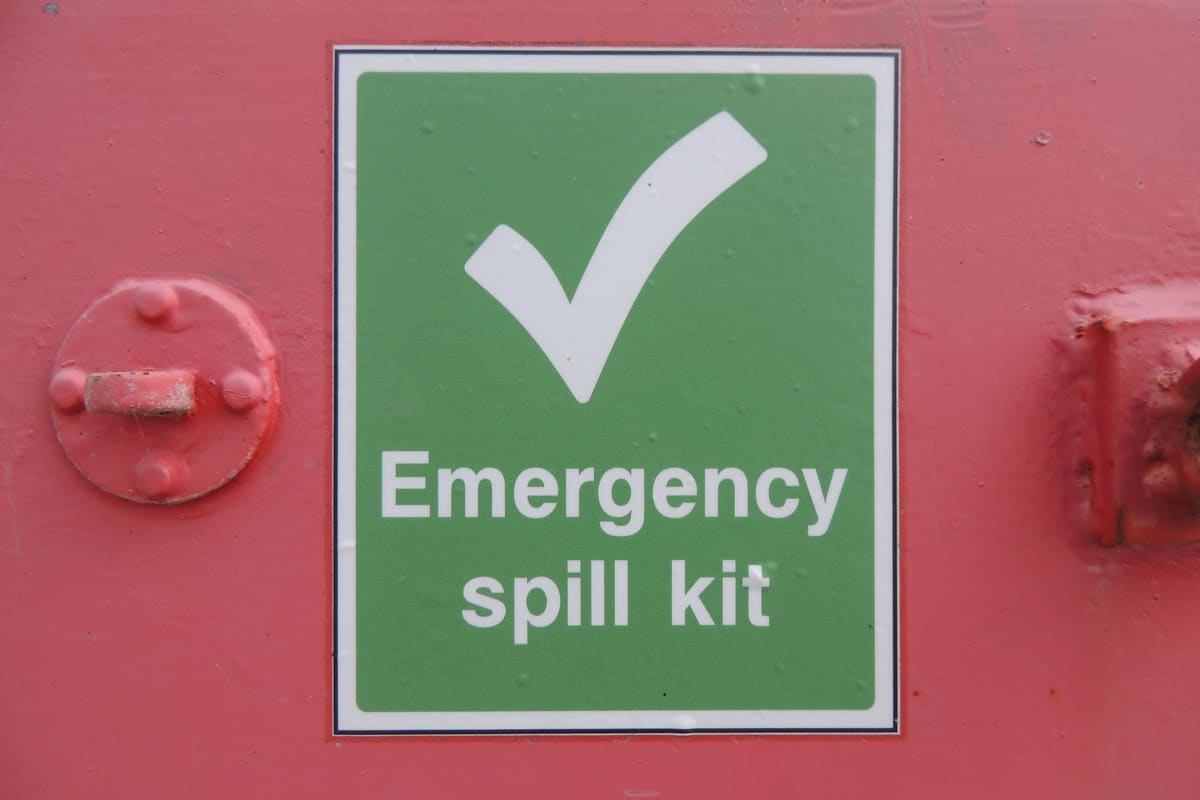
What Is A Spill Kit?
A spill kit contains a collection of spill cleanup materials and tools. Items like absorbent pads, containment dikes and hazardous waste disposal bags. Its purpose is to help confine, contain, and clean up spills that may occur in the workplace.
Spill control kits also contain PPE (personal protective equipment). The level of PPE included in the kit contents varies according to the nature of the spill. Such as water-based liquids versus more hazardous substances like corrosive chemicals.
Basic protective equipment includes gloves and safety goggles to cover the spill responders’ hands and eye areas. Additional hazmat protection—a full body suit, apron or respirator—may be necessary for specialized emergency response kits. For example, spill clean ups involving biohazard materials (think blood) or other hazardous chemicals (think acids).
In short, spill response kits are an important tool for workplace safety. Keeping one onsite can help facilities meet regulations set by the Occupational Safety and Health Administration (OSHA) and the Environmental Protection Agency (EPA).
Emergency Spill Kit Types & Uses
There are many different types of spill kits, including various size and absorbent color options. They can be small and portable enough to tuck inside the cab of a truck or forklift. All the way up to large spill carts on wheels that can absorb more than 100 gallons of fluid.
Among the main varieties are:
- Chemical spill kit: These include yellow sorbents and other items to soak up and contain chemical spills. Sometimes they also have substances that neutralize chemicals so that they are no longer harmful. You may find them in factories or other industrial settings that handle and store chemicals.
- Oil spill kit: Used to contain hydrocarbon spills, these kits often come in large containers capable of handling oil leaks from drums. The sorbents are typically white and float because they repel water. Meaning they are popular kits for water-based sites like marinas, as well as automotive shops.
- Water/universal spill kit: The absorbents in these kits are sometimes called universal because they will work on a variety of spills. Such as water-based liquids as well as oils or solvents. Because they are so versatile, universal kits are popular option for a wide range of business types.
- Specialty spill kits: Including body fluid, battery acid, or liquid mercury spillages. These kits often contain specialized items, such as respirator PPE, to safeguard responders. That’s because body fluids like blood are considered a biohazard and can be highly infectious. Bodily fluid spill kits also contain disinfectants and hazardous waste disposal bags. They are commonly found in hospitals. Kits for battery acid spills are prevalent in vehicle maintenance and parts businesses. Meanwhile, kits for mercury spills are typical to labs.
How Regularly Should You Inspect A Spill Response Kit?
Generally speaking, facilities should have a regular schedule for checking spill kits every one to six months. This applies for all types of spill kits; specialty, hazardous chemicals, oil, or universal.
However, this inspection frequency can depend on whether the spill clean up kit is sealed or unsealed. And that’s because supplies in unsealed kits can sometimes become a target to deal with general cleaning or maintenance tasks (although it’s critical to train employees not to use them for this!). Meaning more frequent inspections may be necessary.
Sealed kits feature a tamperproof sticker or label around the container’s lid. It provides quick visual verification on whether the kit has been opened or not. Which means if the seal—and the container itself—is intact, so are the contents inside.
That said, it is still a good idea to break the seal once or twice a year. For instance, to make sure the kit contents haven’t degraded or expired. Just remember to record the date the seal was broken/replaced for your environmental health and safety (EHS) compliance and audit records.
Often kit inspection tasks fall to the employees responsible for EHS within a business. And can be carried out alongside inspections of other safety equipment; for instance fire extinguishers, first aid, or eyewash stations.
How Do You Check A Spill Containment Kit?
It can be helpful to have a spill kit checklist to follow while you work through your inspection. You can print a separate list for each spill control kit kept onsite.
This document should cover everything the kit is supposed to contain, the quantity of each item, and its condition. For example, absorbent pads, booms, or pillows, along with PPE. You can use the checklist to note down any corrective action that may be necessary, like replacing absorbents.
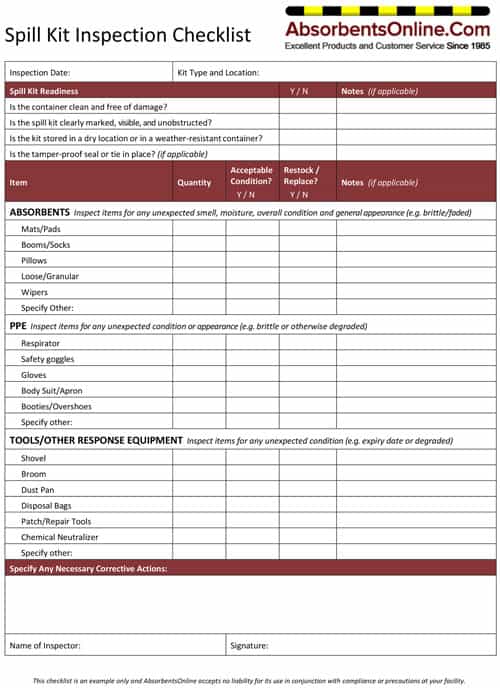
With that in mind, here’s an overview of the steps to follow to check the status of your spill kit:
1. Start by checking the outside of the container itself
Look for cracks, leaks, and holes. Make sure that the lid is secure and tight. The container should be dry, clean, and free of contaminants like mold, dust, or debris. If the kit has a seal, you should verify it remains intact and hasn’t been tampered with. Likewise, the kit’s identification label needs to be in place, without peeling edges.
When a container is damaged, there’s a chance items inside are too (or, may have fallen out).
2. Next, inspect the contents inside the kit
Examine each individual item the kit contains. You want to ensure there is no discoloration, strange smell, or other material degradation which could affect intended use. Verify the expiry date remains valid for things like chemical neutralizers or patching repair tools. If you find any waste or unexpected piece in the kit, be sure to remove it.
Over time, things like gloves or waste bags can become brittle and ineffective. Especially when kits are kept in locations exposed to extreme hot or cold temperatures. These items may need replacing
3. Verify the kit and/or its signage remains legible and visible
Depending on the location your spill response kit is kept, it’s possible other items may obstruct its accessibility. For instance, when mobile kits are stored under a workbench or elsewhere on a warehouse floor. Relocate clutter, or other items like brooms or boxes, if they have been shifted in or around the kit’s container.
For kits using additional wall or floor signage identification, check that the lettering is not worn or faded.
4. Finally, take any necessary actions
If you spot something wrong with the kit, record and report it per your company’s EHS procedures. This may include filing a signed and dated copy of your inspection checklist for audit purposes. Should you find any missing, expired or degraded parts, aim to replace or restock them as soon as possible.
Frequently Asked Questions
Why Is Checking A Spill Kit Important?
In short, inspections are necessary to maintain best practices for the health and safety of people and plant. If a spill kit doesn’t remain in good condition, and with the right supplies, then it is useless. Reason enough for your facility to undertake regular spill kit inspections!
What Happens If I Fail To Inspect My Kit?
Neither OSHA nor EPA regulations require spill kit inspections or dictate how frequently you should check them. However, if you fail to inspect your kit, then you risk it not being usable in the event of an emergency spill. The outcome being potential injury, damage, or—worst case scenario—a fine.
How Long Does A Spill Kit Last?
A spill kit lasts for roughly 5 years. However, it is recommended that you routinely change the products in your kit to maintain material performance.
To prolong a kit’s shelf life, be sure to store it in climate controlled conditions. For instance, without exposure to moisture, humidity, or harsh weather elements.
Final Thoughts
Having a spill kit to prepare for a potential spillage or hazardous material clean up is common for many businesses. Although, it is necessary to inspect them regularly: at least twice a year, but possibly monthly or more frequently. This will ensure the contents are working correctly and help to avoid spill accidents or injuries.
Does your emergency response kit need replacing or the items inside require restocking? Explore a large selection of spill containment supplies and kits at AbsorbentsOnline.com.