Temporary floating containment for oil spills
An oil containment boom is a large, maneuverable flotation device that’s used to contain an oil or chemical spill within a water area. They help reduce the potential for environmental pollution and assist in recovery operations (using collection equipment like skimmers and vacuums).
Oil is less dense than water, giving it buoyant properties. That means when oil releases into the ocean, it naturally floats to the surface rather than sink to the bottom or hover in the middle. This makes containment booms highly effective at creating a barrier that traps oil in a thick layer on the water’s surface. Any oil that releases into water will travel to the surface where booms are waiting to contain it.
With that said, oil spreads fast on the surface when it’s not contained. The longer first responders wait to deploy oil spill containment booms around the perimeter, the larger the spill area will become. This is why it’s important for response crews to work fast during the initial hours of an oil spill.
After surveying the situation, first responders will layout a perimeter of booms to contain the oil. The goal when dealing with a spill is to create a full circle of booms with no openings or gaps. Once the boom circle is complete, the oil will remain trapped inside where it can no longer continue to spread.
What are oil booms made of?
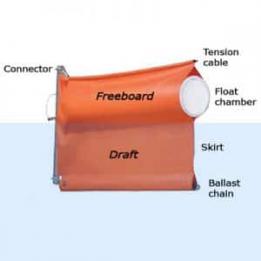
Oil containment boom components showing how it works
Booms feature several heavy duty components to stand up to tough marine environments. Impermeable PVC is a high strength fabric common to most booms, often a bright yellow or orange for high visibility. It acts as a skin around the foam flotation chamber which sits above the water surface (the freeboard). Boom floats provide buoyancy and come in different shapes, including flat rectangular (fence booms) or round cylinders (curtain booms).
PVC also forms the skirt that sits in the water and acts as the barrier wall beneath the surface. A ballast chain at the base of the skirt provides weight and bottom tension. This section is known as the boom’s draft.
Slide connectors and pins run down the total height of the boom, linking sections together to form the enclosure shape. Some booms use a tension cable that runs along the top of the freeboard, to provide extra strength in rough water conditions.
Where are oil spill booms in use?
Approximately 1/3 of the world’s oil comes from offshore drilling sites. While most offshore rigs never run into any problems, unfortunately, on occasion damage to either the structure or drill itself results in oil spilling into the ocean. One example that’s all too familiar is the Gulf of Mexico’s infamous Deepwater Horizon oil spill of 2010.
The number one combat system against spills such as this is the deployment of oil spill containment booms. In both the United States and other countries, regulations require such pieces of equipment are readily available in the event of an unexpected spill.
Boom spill response and control
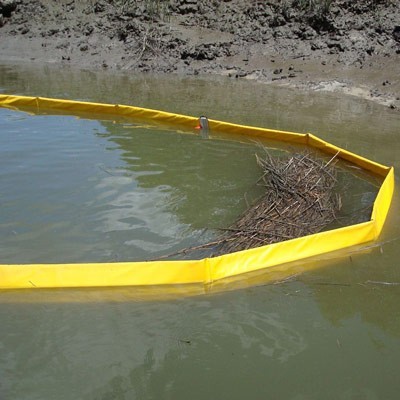
Containment booms trap oil and marine debris
Containment booms aren’t meant to clean up oil spills. Instead, their purpose is to contain them. Once the spill area is contained, the cleanup crew will then decide on the best course of action to remove the oil. Recovery equipment like oil skimmer machines pull oil from the surface where it’s collected in storage tank containers.
In the Deepwater Horizon spill, hundreds of skimming machines were used to clean up the murky Gulf waters. It also took nearly an 800 mile stretch of oil containment booms to corral the enormous spill.
But accidental spills don’t only happen at sea, they occur in other bodies of water as well. This includes chemical spills into rivers, stormwater discharge in lakes, and oil leaks from boats in canals. Booms can offer effective spill containment and spill control solutions in all these scenarios.
ASTM boom guidelines offer information on selecting equipment for different water body classifications.
Different water areas call for different booms
Oil containment booms come in various shapes, sizes and have specific applications for different water conditions. For example, in fast water environments—like rivers and bays—a high tensile strength boom is necessary. Typically, these booms use a heavy duty tension cable to increase resistance against strong currents. A top tension cable also ensures the boom remains secure in windy conditions and water movement due to boat traffic wakes.
In protected or calm waters (such as streams, swamps and ditches), it is possible to deploy a more lightweight boom design. In these water locations a fence boom with floating flat panels may be an appropriate solution for oil spill response. These structures are often quick to deploy, and compact to store or transport.
Booms are usually available with different height freeboards above the water line. These help keep materials within the boom and reduce splash over for better spill control. Depending on the environment, anchor kits or buoy boom accessories can often assist in deploying and installing an oil boom.
Absorbent vs. Oil Booms
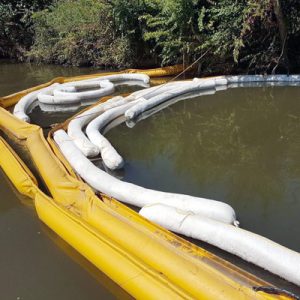
Oil containment (yellow) and absorbent booms (white) can work well together
Some spill cleanup crews may use absorbent booms rather than oil containment booms. Basically, absorbent booms are designed to contain and absorb oil. When the booms are full of oil, they will continue to float on the surface of the water until a crew members picks them up.
Although oil absorbent booms offer a quick and easy way to clean up oil, some crews prefer the simplicity of basic oil spill containment booms. This is particularly the case with recovery operations where oil collection for re-use is the primary objective.
Because both varieties float, it is also an option to use oil absorbent booms (and other oil absorbing products) together to clean up spills.
An oil containment boom is a large, maneuverable flotation device that’s used to contain an oil or chemical spill within a water area. Prepare your business and team to deal with a boat engine leak or spill before it becomes an environmental risk. Talk to AbsorbentsOnline for advice about oil absorbing socks, pads and pillows for marine spills. We’re here to help!
This is a revision to a post with an original publish date of August 29, 2013.